Comparing Arc Welding to Other Welding Methods: Pros and Cons
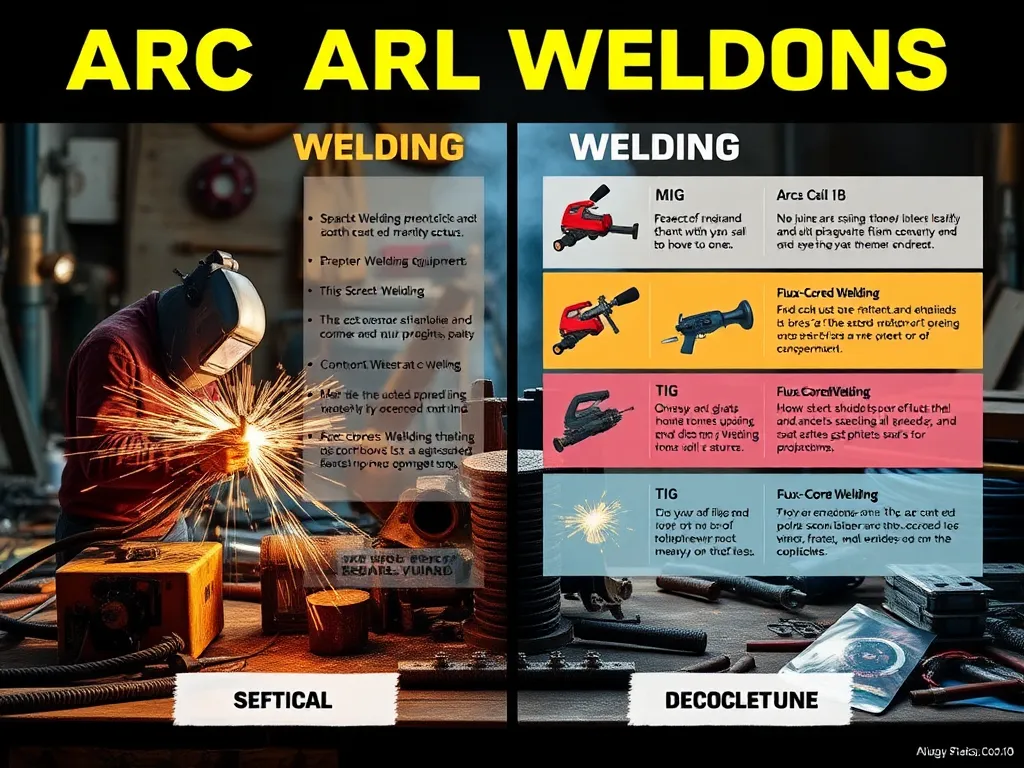
Comprehensive Guide to Welding Methods
Welding methods encompass various techniques used to join materials, primarily metals, through the application of heat, pressure, or both. This process is crucial in a wide range of industries, from construction to automotive manufacturing, as it creates strong, durable connections. The choice of welding method depends on factors like the material type, thickness, and the specific requirements of a project.
Effective welding method selection takes into account the materials involved, desired strength, and application environment.
There are several welding methods available, each with its unique advantages and applications. Some popular techniques include arc welding, MIG (Metal Inert Gas) welding, TIG (Tungsten Inert Gas) welding, and spot welding. Understanding these methods and their differences is key to selecting the right approach for any given task.
The fundamentals of welding methods involve the use of heat to melt the base materials and, in many cases, a filler material that helps to form a strong joint once cooled. Welding can be performed in various environments, including open air, underwater, or in controlled workshops, making it a versatile solution for many industrial needs.
Each welding method has its specific procedure, including equipment setup, welding rods or filler material used, and post-welding treatments. As industries evolve, so do welding techniques, with innovations that improve efficiency, safety, and the quality of welds being introduced regularly.
A thorough MIG comparison is essential for choosing the right technique for your welding needs.
The future of welding methods is also promising, with advancements like robotic welding and automation shaping how manufacturing processes are executed. These innovations offer enhanced precision and consistency, meeting the increasing demands of modern applications.
Understanding the differences between arc vs laser welding can significantly affect project outcomes and material suitability.
Advantages of Arc Welding
Arc welding offers high versatility in applications across different industries. It can be employed for various tasks, such as repair work, heavy fabrication, and even delicate jobs, depending on the specific type of arc welding technique used.
One of its significant benefits is the ability to weld thick materials effectively. The intense heat generated makes it possible to join materials that are more substantial than other welding methods can accommodate.
Arc welding is also cost-effective for mass production processes, as it allows for faster welding speeds and less material waste compared to other techniques, making it ideal for large-scale applications.
Another advantage is the good penetration and fusion of metals that arc welding provides. This ensures strong joints, capable of withstanding high levels of stress and environmental impacts.
Disadvantages of Arc Welding
Despite its advantages, arc welding has its limitations. It is somewhat limited to specific environments, as factors like wind can influence the quality of the weld, particularly in outdoor applications.
Furthermore, arc welding requires skilled operators to prevent defects. Lack of experience can lead to issues such as improper penetration, inconsistent weld beads, or overall weak joints.
Another downside is that it can be slower compared to some other welding methods. This might not be suitable for all applications, particularly when speed is a crucial factor.
Weld splatter and clean-up issues can also arise with arc welding. The molten metal can result in spatter, requiring additional time and effort for cleaning up and finishing the weld area post-operation.
Comparison with MIG Welding
When comparing arc welding with MIG welding, one can note significant differences in equipment setup and cost. MIG welding utilizes a spool of welding wire, which requires a specific setup, leading to differences in initial investments and operational expenses.
Regarding speed and efficiency, MIG welding typically offers faster processes compared to traditional arc welding. This efficiency can be critical in high-production environments where minimizing downtime is essential.
Metal compatibility and thickness also vary between the two methods. While both can handle a range of materials, MIG welding can be more effective for thinner materials, while arc welding excels in thicker metal applications.
In terms of application scenarios, MIG welding is often used in industries like automotive or manufacturing due to its speed, whereas arc welding finds its place in heavy machinery or construction projects where strength is essential.
Comparison with TIG Welding
When comparing TIG welding to arc welding, the distinction lies largely in the precision and control of the welding process. TIG welding offers more intricate control over the weld, making it ideal for detailed and delicate work or aesthetically demanding applications.
Material types and thickness capabilities differ, as TIG welding can be used on a wider variety of materials without the need for filler rods, often allowing for stronger joints with thinner materials than those typically tackled by arc welding.
Training requirements and skill levels for TIG welding are generally higher than for arc welding. TIG welders need to master specific techniques and processes, making it a more specialized and potentially slower method for skilled laborers.
The heat-affected zone (HAZ) in TIG welding is typically smaller compared to arc welding, which can be advantageous for projects requiring minimal distortion and heat damage to surrounding materials.
Comparison with Spot Welding
Spot welding is highly suitable for applications in industries like automotive manufacturing, where it is frequently used to join overlapping sheets of metal. This method is efficient and provides quick welds for production lines.
In terms of speed vs. strength considerations, while spot welding offers rapid production capabilities, it may not always match the strength that can be achieved through traditional arc welding, especially for larger structures.
Equipment differences are notable too, as spot welding machines are typically less complex than those required for arc welding, potentially leading to lower investment costs upfront.
Finally, weld quality and testing methods differ between spot and arc welding, with spot welds often requiring different inspection procedures to ensure that the welds meet the necessary specifications and standards.