Understanding MIG: What Does MIG Stand for in Welding?
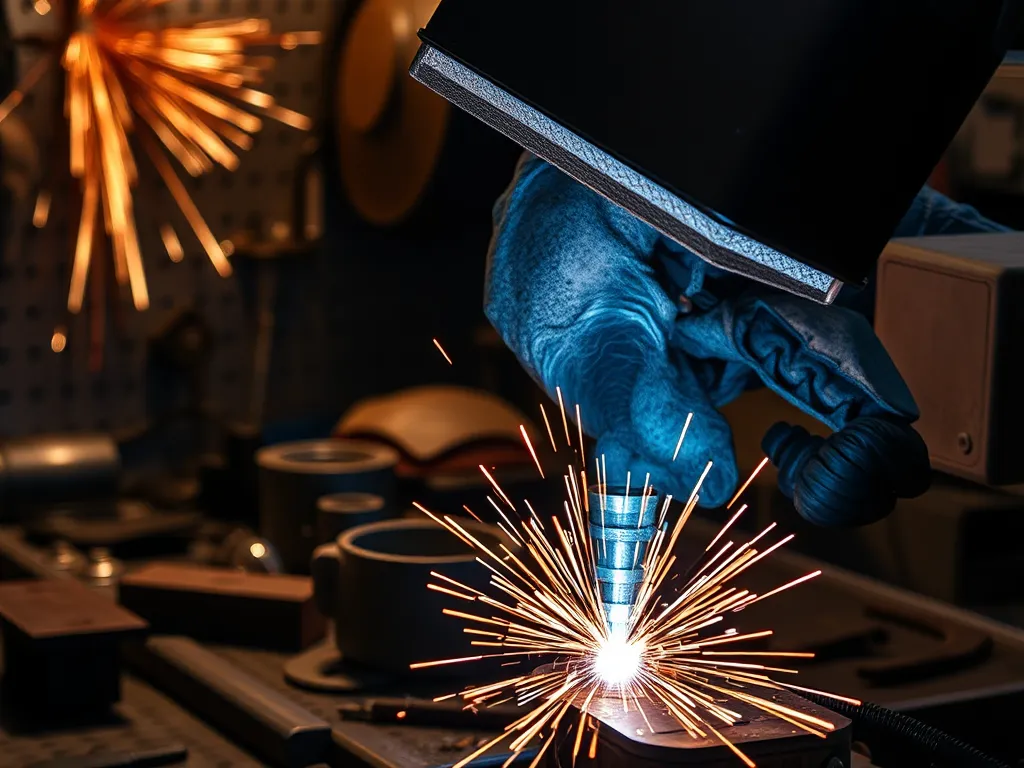
A Comprehensive Guide to MIG Welding
MIG Welding, which stands for Metal Inert Gas Welding, is a popular welding process that uses a continuous feed of a filler metal electrode and an inert gas to protect the weld pool from contamination. This method is favored for its speed and versatility, making it a go-to choice for many welding professionals and hobbyists alike.
The process of MIG Welding is particularly well-suited for thicker materials, and it is commonly utilized in a range of industries, from automotive to construction. The adaptability of MIG Welding allows it to be effective on various types of metals, including steel, aluminum, and stainless steel, contributing to its widespread popularity.
A major advantage of MIG Welding is its ease of use, which makes it accessible for beginners in welding. The ability to perform the welding process in all positions, combined with its higher deposition rates, enables welders to complete projects more quickly than with other types of welding.
In addition to its user-friendly nature, MIG Welding exhibits outstanding quality due to its ability to produce clean and precise welds. This quality is essential for critical applications where material integrity is paramount. As such, MIG Welding continues to be an indispensable technique in welding today.
Dive into the GMAW process terminology with this informative guide.
Overall, MIG Welding represents a fusion of technology and artistry in the realm of metalworking, making it a central aspect of manufacturing and fabrication across a variety of sectors.
This link provides a clear MIG welding explanation, ideal for beginners.
Definition and Meaning of MIG
The term MIG stands for Metal Inert Gas. The process utilizes a spool of wire that acts as an electrode, feeding continuously into the welding torch. The inert gas, usually a mixture of argon and carbon dioxide, acts as a shield, providing protection against atmospheric contamination that could compromise the weld quality.
MIG welding was developed in the 1940s and 1950s as a response to the need for efficient and effective welding techniques. It gained prominence after World War II, as industries began to explore new methods for joining metals, resulting in the widespread adoption of the process.
For a thorough Metal Inert Gas definition, visit this resource.
Unlike other welding methods such as TIG (Tungsten Inert Gas) welding or stick welding (SMAW), MIG welding offers a continuous feed of filler material and is generally easier to learn and operate. This has made MIG the preferred choice for many applications requiring speed and efficiency.
MIG Welding Process
The MIG welding process works by creating an electric arc between the continuous wire electrode and the base material. As the wire melts, it fills the joint while the inert gas shields the weld pool from contaminants in the air. This process allows for a strong and clean weld.
To carry out MIG welding, one requires specific equipment, including a MIG welding machine, a continuous spool of wire, a welding gun, and a supply of inert gas. Safety gear, such as welding helmets and gloves, is also necessary to protect against harmful UV rays and heat.
Common techniques in MIG welding include short circuit transfer, globular transfer, and spray transfer. Each technique is employed based on the thickness and type of materials being joined, as well as the desired characteristics of the weld. Adjusting parameters such as voltage and wire feed speed can significantly affect the outcome of the weld.
Advantages of MIG Welding
The benefits of MIG welding include its speed, versatility, and ease of use. The continuous wire feed allows for longer welds without the need for frequent electrode changes, and its adaptability means it can be used across various materials and thicknesses.
MIG welding is known for its efficiency and speed; it can produce welds faster than many other welding methods. This can result in substantial time savings in manufacturing processes, making it an attractive option for businesses seeking to improve productivity.
Cost-effectiveness is another attribute of MIG welding techniques. The efficiency of the process reduces overall labor costs while minimizing material wastage. Additionally, the equipment for MIG welding can often be less expensive than other welding setups, contributing to lower initial investments for businesses.
Applications of MIG Welding
MIG welding is widely used across various industries, including automotive, aerospace, construction, and shipbuilding. Its adaptability and efficiency make it ideal for mass-production environments, where speed and consistency are essential.
Real-world projects utilizing MIG welding can range from constructing large structures to fabricating intricate components. The flexibility of the MIG welding process allows for both small-scale and large-scale operations to benefit from its technology.
In the automotive manufacturing industry, MIG welding plays a crucial role in assembling vehicle frames and body parts. The speed and strength of MIG welds make it suitable for high-volume production lines, leading to increased efficiency in vehicle assembly.
Common Mistakes in MIG Welding
Beginners in MIG welding often make frequent errors such as incorrect settings on the welding machine or improper technique. Common mistakes include welding too slowly, resulting in excessive heat and burn-through, or too quickly, which can cause weak welds or poor penetration.
To troubleshoot issues in MIG welding, it's vital to check machine settings, including voltage and wire feed speed, and ensure proper shielding gas flow is maintained. Additionally, examining the condition of the wire and ensuring it's clean can prevent many common defects.
Improving MIG welding skills involves practice, seeking education through workshops or online resources, and learning from mistakes. Regularly evaluating welding techniques and experimenting with different settings can help welders refine their skills and achieve higher-quality results.